How has the military placed technology at the heart of aviation sustainment? (Studio)
Brought to you in partnership with Collins Aerospace
Major military operators and industry experts place technology at the centre of their future strategies, in everything from digitalisation to open systems architectures (OSAs).
An effective strategy will rely on the partnership between a high-performing supply and manufacturing base and a flexible and innovative customer. This alliance will manage obsolescence and gain maximum advantage in future upgrades, according to the experts.
Technological and operational innovations today provide significant resources to overcome sustainment challenges.
Jeffrey Sick is director of logistics at the US Air Force Sustainment Center.
He pointed to Agile Combat Employment (ACE) techniques, which the USAF terms ‘a proactive and reactive operational scheme of manoeuvre executed within threat timelines to increase survivability while generating combat power throughout the integrated deterrence continuum’.
According to Sick, this leads to a “push” rather than “pull” system. It provides a decisive advantage and enables the USAF ‘to communicate with our different forward-based units and provide the supplies and the parts and the capabilities they need, at the right place and at the right time’.
The air force is looking at agile facilities, hangars and other capabilities to provide support to various weapon systems, Sick added, no matter their size, bandwidth or cyber capabilities. He also pointed to software as a critical focus ‘as we move from the analogue space to the digital world’.
To make such goals a reality, militaries and industry must boost their collaborative efforts.
The Royal Netherlands Air Force (RNLAF) is benefiting from such an approach through its work with Collins Aerospace. The partners have established a Pilot Readiness Centre in the Netherlands, the first such centre outside the US.
Lt Col Ted Meeuwsen, the RNLAF’s deputy commander of the Center for Man in Aviation, highlights the benefits collaboration through the case study of F-35 pilot helmets.
Previously, if something went wrong with the helmets, ‘we had to send it over to the US’ to be fixed. However, he argued that this is ‘not wise at all. That’s not efficient – you cannot fly for five weeks or so’.
The centre means the RNLAF can address such problems at home in collaboration with Collins Aerospace.
For Collins Aerospace, OSAs are a critical technological element in the evolution of sustainment.
‘The idea is to allow customers, suppliers and others to have insight into the system,’ explained Jeffry Howington, principal business development manager at Collins Aerospace.
‘Such that they can place capabilities into the system without having to go into any kind of specialised education about how the system was constructed or the interfaces it’s using,’
OSAs help get new capabilities into the field as fast as possible, Howington said. For government users, it means ‘they can now counter those rapidly changing threats which characterise the modern battlespace’.
This has long been a focus for Collins Aerospace, Howington added, from the KC-135 to the CH-53K. The company is also pursuing such efforts through industry groups like the Open Group Future Airborne Capability Environment (FACE), which develops open architecture standards in the aviation domain.
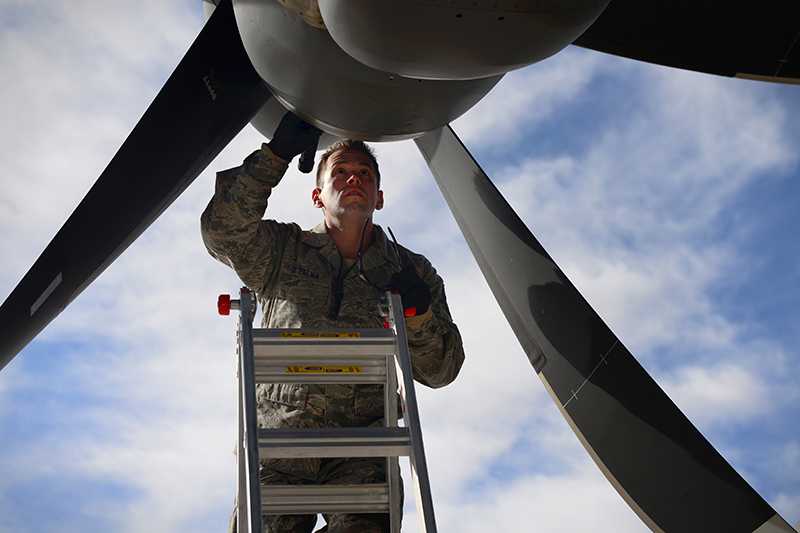
While OSA technology is developing quickly, the essential aim is nothing new: improving aircraft readiness.
Brian Kruger, senior director of commercial and military services sales at Collins Aerospace, said OSAs allow operators to be nimbler.
‘And listening to the customers allows us to mitigate and change our systems to have upgrades that are quicker and more easily done. You’re doing a percentage of the aircraft at the time, instead of the entire aircraft,’ Kruger explained.
Militaries rely on a digital backbone to support and enhance their sustainment strategies and ensure fleet readiness, Howington noted. This provides ‘the framework within a system to allow for easily updating and bringing in new technologies’.
There are two aspects to this, he said: the digital backbone, which incorporates networking and computing resources; and the framework to ‘plug in’ the software, based on concepts like FACE.
Digital maintenance technologies offer significant benefits in this environment.
For Bell, this is tied to the concept of a “digital thread”. Mike Moody, the company’s manager for integrated product support for the Future Vertical Lift (FVL) programme, outlined the benefits of this approach.
‘This allows us to connect and to use original source data by all the downstream consumers of that data, so you don’t have to repackage data that originated in a design environment and then repackage it for maintenance manuals, repackage it for instructions to the fleet, repackage it for technical manuals,’ Moody said.
‘It’s all the same data, so that accuracy is improved, the speed of distribution is improved.’
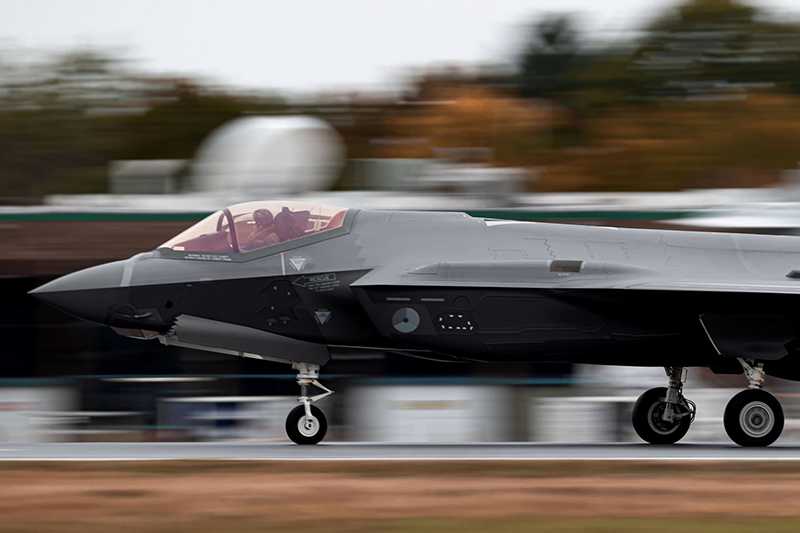
The relationship between industry and government will only grow more critical in the coming years and decades. How can this relationship be utilised more effectively?
‘I would say that the military and industry together need to assess the potential operational scenarios of the system or aircraft platform,’ said Kruger.
‘Is it a training situation versus a mission or different types of missions? Collins would help listen, and adjust the assumptions, evaluate the risks, and help our military build a more flexible, performance-based programme that adapts with the use of the asset.’
But even as technologies evolve along with the logistics processes to sustain them, it’s crucial to keep the human dimension at the centre of our thinking.
Col Meeuwsen noted that while modern airframes like the F-35 measure the performance of everything in the platform, the same isn’t true of the human onboard. He said the Netherlands and other countries are trying to speed up this innovation cycle.
‘We want to know how people perform,’ he said, from eye-tracking to heart and lung performance.
‘Especially when you want to look into man-machine teaming, you have to know if people perform in a better way using new technology or in a worse way, for instance. So that’s exciting.’
More from The Critical Care podcast
-
Podcast: Critical Care episode 4 - The operator's view
Welcome to Episode 4 of Shephard Studio’s Critical Care podcast, the story of military aircraft sustainment and support in an unpredictable world.
-
How can strong industrial partnerships help to enhance fleet readiness? (Studio)
To adapt to an unpredictable future, military aircraft operators must partner closely with industry, accessing the resources and flexibility they need in a rapidly evolving operational environment.
-
Podcast: Critical Care episode 3 - Finding the value in military-industry partnerships
Welcome to Episode 3 of Shephard Studio’s Critical Care podcast, the story of military aircraft sustainment and support in an unpredictable world.
-
OEMs embrace a tailored approach to sustainment (Studio)
At a time of rising peer and near-peer threats, enduring force readiness has never been more important for western militaries.
-
Podcast: Critical Care episode 2 - Delivering a tailored approach to aircraft sustainment
Welcome to Episode 2 of Shephard Studio’s Critical Care podcast, the story of military aircraft sustainment and support in an unpredictable world.
-
Collins Aerospace keeps B-52 bomber flying
Collins Aerospace has joined the effort to keep the B-52 Stratofortress in service.