RCV-Pioneer Mobility, Counter-Mobility and Survivability on demand for Remote and Autonomous Vehicles (sponsored)
This article is brought to you by Pearson Engineering
RCVs look set to take a prominent position in the configuration of military land forces in future conflict, progressively taking humans away from ‘dull, dangerous and dirty’ tasks, and affording skilled personnel the time and safety to outwit adversaries.
Regardless of mission, the fact remains, that these vehicles will need to move to places of their Commander’s choosing and in doing so, will need to defeat the wide range of natural and deliberate obstacles usually encountered on the battlefield. An RCV without protection may still be subject to enemy action, if not to injure soldiers, but to stop valuable assets in their tracks.
RCV-Pioneer – Scalable Battlefield Mobility
In response, Pearson Engineering has developed RCV-Pioneer, a new approach to the integration of mobility, counter-mobility and survivability equipment for robotic vehicles. Based on the same core principles of rapid interchangeability and agility, which are present throughout Pearson Engineering’s product range, RCV-Pioneer provides remotely controlled engineering capability to RCVs. This allows such vehicles to scale and optimise for the task at hand, whether to support its own mobility, or to provide an engineering effect for others.
It is a self-contained, pre-configured frame to which Pearson Engineering’s combat engineering equipment can be integrated to support specific missions. Such equipment is provided by palletised Mission Packs including capability for obstacle clearance, route proving, minefield breaching and assault gap crossing which can be rapidly swapped out in field conditions.
RCV-Pioneer uses an innovative self-lifting system to allow RCVs to rapidly manoeuvre underneath mission packs for rapid integration and removal. RCV-Pioneer mounts to the host platform using quick release fastenings, which require no tools to operate, allowing it to be rapidly fitted and removed from the RCV. The system design will allow two soldiers to fit or remove RCV-Pioneer from the RCV in approximately 30 minutes.
RCV-Pioneer does not require any hydraulic power from the host platform and comprises all the required hydraulic controls for its mission specific tools such as ploughs, dozer blades and excavator arms. It can either take electrical power from the host RCV platform or generate all required power using an integral diesel engine.
The RCV-Pioneer Mission Packs are remotely controlled using an intuitive Operator Control Unit (OCU) which includes joysticks and touch screen controls to manage all of its functions. The OCU displays video feeds from cameras mounted on RCV-Pioneer to give optimal situational awareness whilst performing engineering tasks.
Mission Packs – Pioneering Products, Proven on the Battlefield
For nearly 40 years, Pearson Engineering has provided equipment to help Armed Forces to defend, move and flight. Our products enable combat forces to breach minefields, to overcome explosive ordnance and to defeat and create obstacles. They are designed to provide armoured vehicles with the ability to rapidly adapt to their mission, to overcome challenges to mobility and to deny mobility and momentum to others.
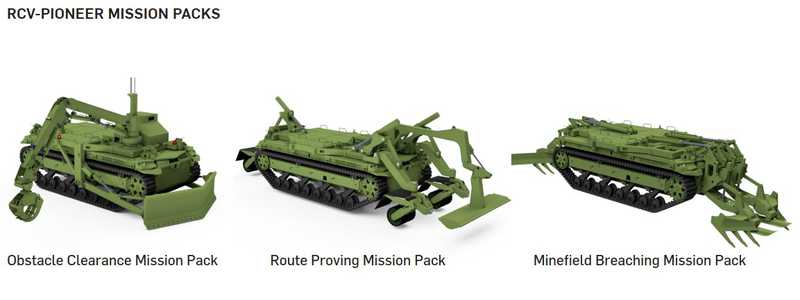
The same approach has been applied to RCVs with mission packs optimised, in the same way as Front-End Equipment (FEE), to deliver against mobility, counter-mobility and survivability tasks.
Manoeuvre Support Sustainment and Protection Integration Experiments (MSSPIX)
A prototype version of RCV-Pioneer + Obstacle Clearance Mission Pack was recently trialled on the General Dynamics Land Systems (GDLS) TRX RCV. It included a manipulator arm capable of lifting objects up to 500kg (1100lbs), a V-shaped dozer blade for moving obstacles, and an area which is designed to carry a variety of different loads. This capability was successfully demonstrated to the US Army at the Manoeuvre Support Sustainment and Protection Integration Experiments (MSSPIX) 2021 at Fort Leonard Wood. A Mine Clearing Line Charge (MICLIC) frame was fitted to the flexible load area for the MSSPIX trial to show an additional capability which could be added in the future.
More from Industry Spotlights
-
How do we detect and defeat enemy drones?
Learn about the portfolio of sensors and effectors for the complete counter-UAS mission at Raytheon, an RTX business.
-
The power of partnership: GDMS–UK deepens cooperation with the British Army
In Conversation: Shephard's Gerrard Cowan talks to General Dynamics Mission Systems–United Kingdom’s Chris Burrows about how the company's UK TacCIS business is reshaping battlefield communications through sustained customer engagement, accelerated innovation and ecosystem collaboration.
-
Expanded focus – unleashing the potential of commercial SATCOM for defence
In conversation... Intelsat's Ray Lindenmayer talks to Shephard's Gerrard Cowan about the new capabilities advanced commercial SATCOM technologies can provide for military customers, and how industry and government can best work together to achieve maximum effect in orbit.
-
Enhancing education: How CAE is embracing new technology to boost military training
In Conversation... Shephard's Gerrard Cowan talks to CAE's Marc-Olivier Sabourin about how the training and simulation industry can help militaries achieve essential levels of readiness by leveraging new technology, innovative procurement methods and a truly collaborative approach.
-
Why tactical UAVs are winning on the future battlefield (Podcast)
In Conversation: In this special edition of the Shephard Defence Podcast, Tony Skinner sits down with Dan Slasky, President and CEO of Aeronautics, to explore how cutting-edge tactical unmanned aerial systems are reshaping today’s battlefields.
-
Fincantieri’s Vulcano Class: a new era of versatility and innovation in naval operations
Logistic support ships (LSS) are essential for sustained naval operations, especially during extended deployments far from home ports.